Field Service Management software for manufacturing excellence
Keep production running with automated maintenance and real-time service coordination. Manufacturers depend on precision, efficiency, and uptime—maintenance should never slow that down. Fieldcode FSM software automates maintenance scheduling, tracks assets in real time, and ensures fast service response to keep production lines running without disruption.
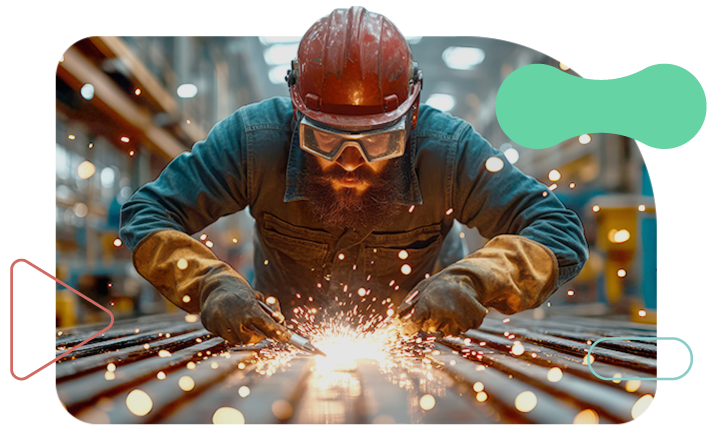
Why manufacturers choose Fieldcode
Essential features for manufacturing maintenance teams
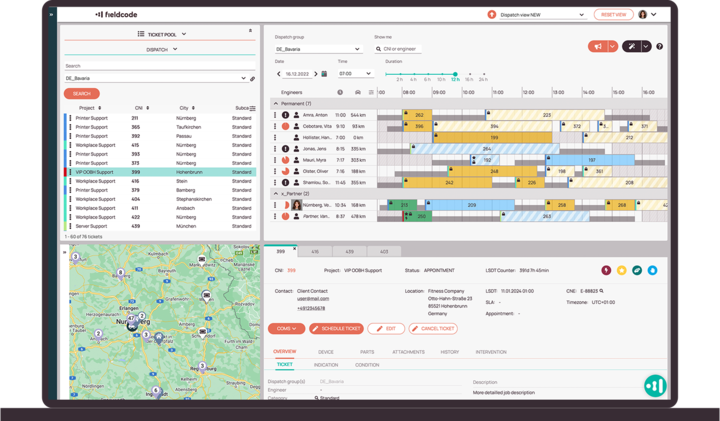
Smart work order management
Schedule, assign, and track maintenance jobs in real time—ensuring machines get serviced before they fail. Automated dispatching ensures the right technician is assigned based on skillset, location, and availability.
Mobile app for field technicians
Equip service teams with instant job details, digital checklists, and offline capabilities to keep repairs on schedule—even in areas with limited connectivity.
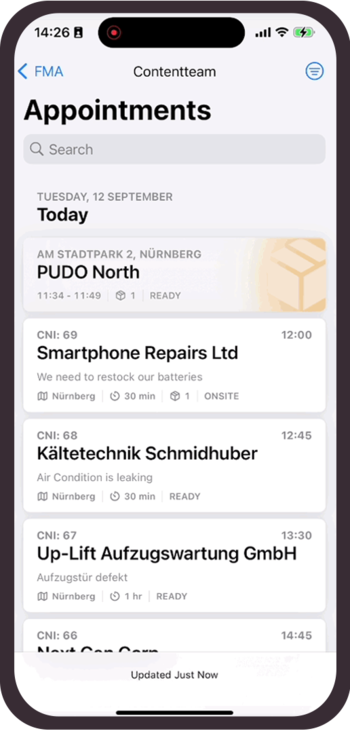
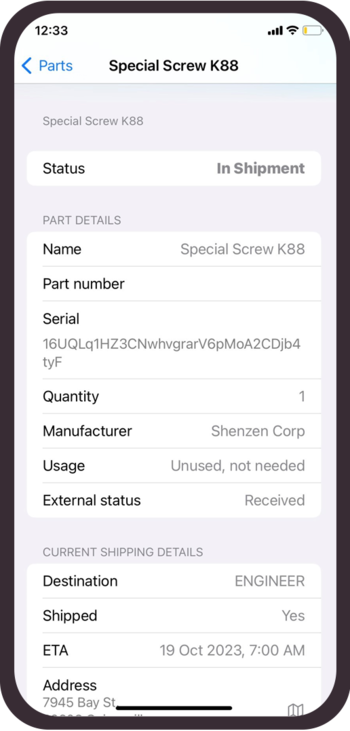
Real-time spare parts and inventory tracking
Keep track of critical spare parts, automate restocking alerts and ensure replacement parts are available before a breakdown occurs.
Centralized maintenance insights and reporting
Monitor work orders, technician performance, and repair costs in real time. Gain actionable insights to reduce maintenance costs and optimize service efficiency.
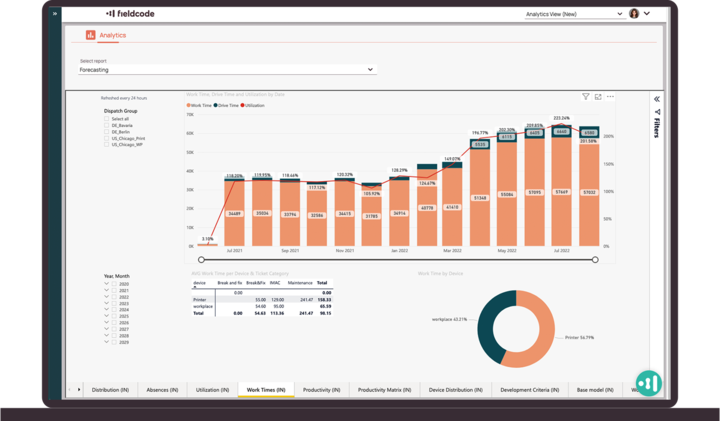
Tools to enhance your maintenance strategy
Planned & preventative maintenance
Automate maintenance scheduling to reduce downtime and extend asset lifespan.
Asset & equipment management
Maintain detailed service records, manage warranties, and optimize maintenance schedules based on contracts or predefined schedules.
Compliance & audit-ready service records
Keep digital maintenance logs to simplify audits and ensure compliance with industry standards.Technicians can attach photos, service reports, and other documents directly to work orders—creating a complete, verifiable maintenance history.
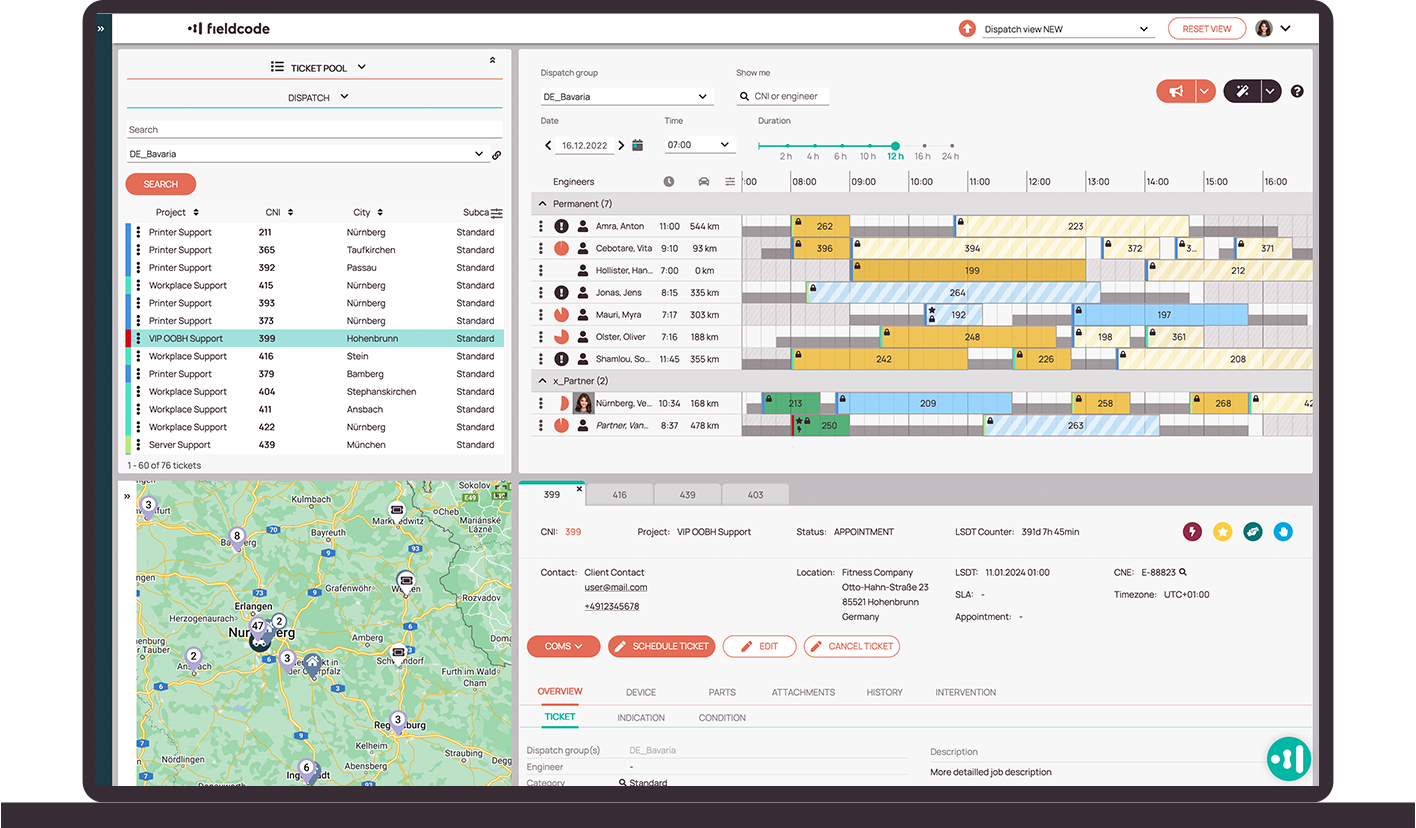
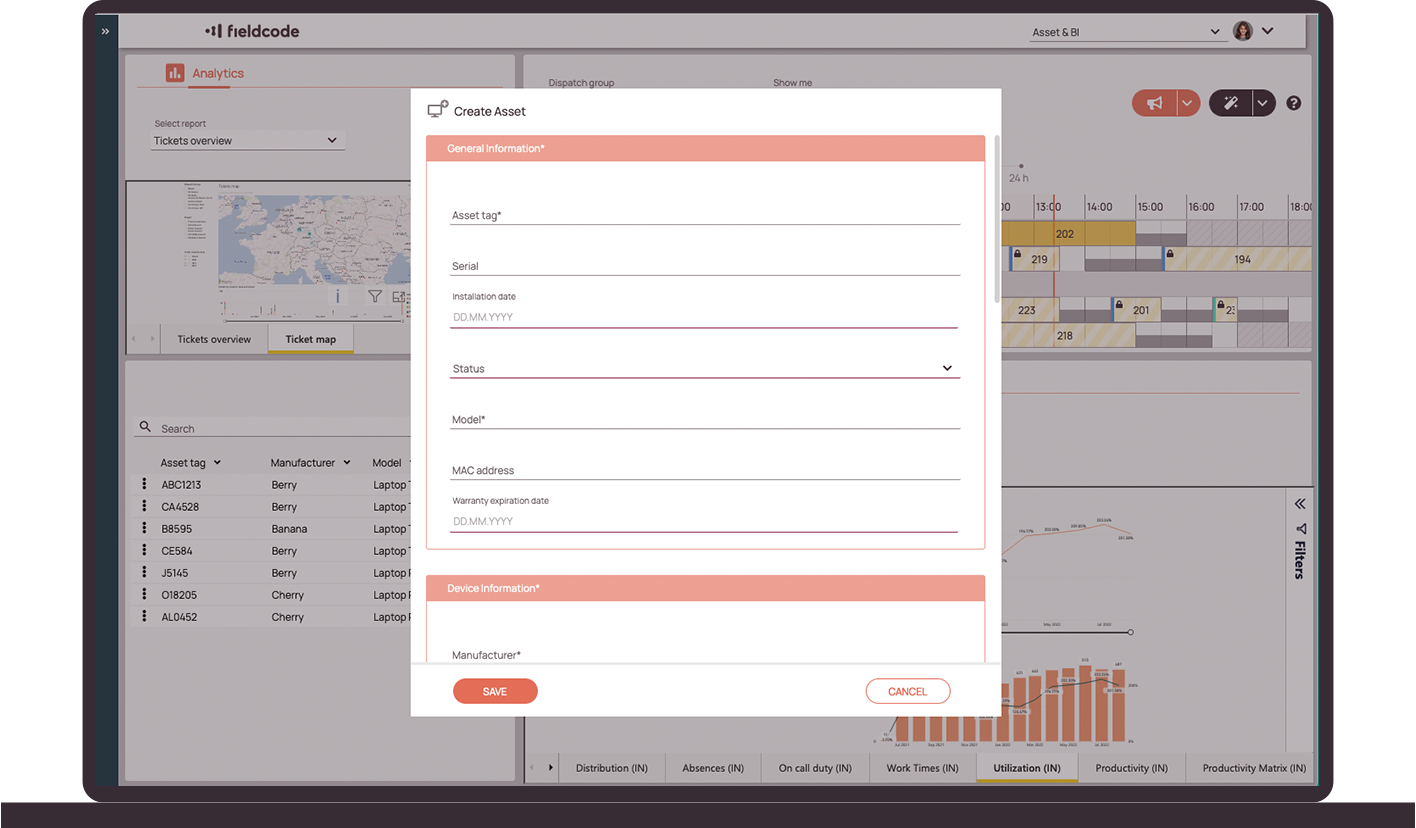
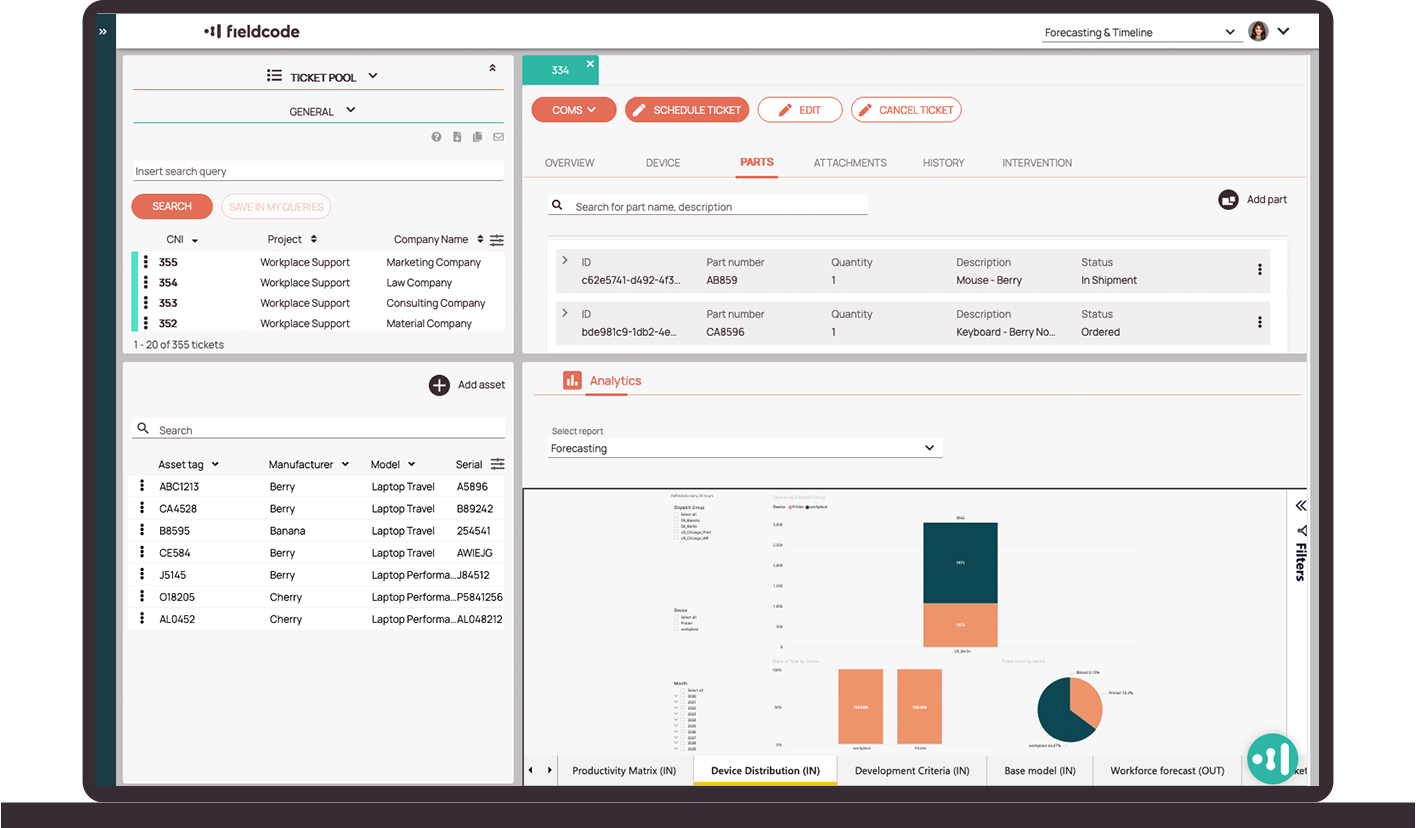
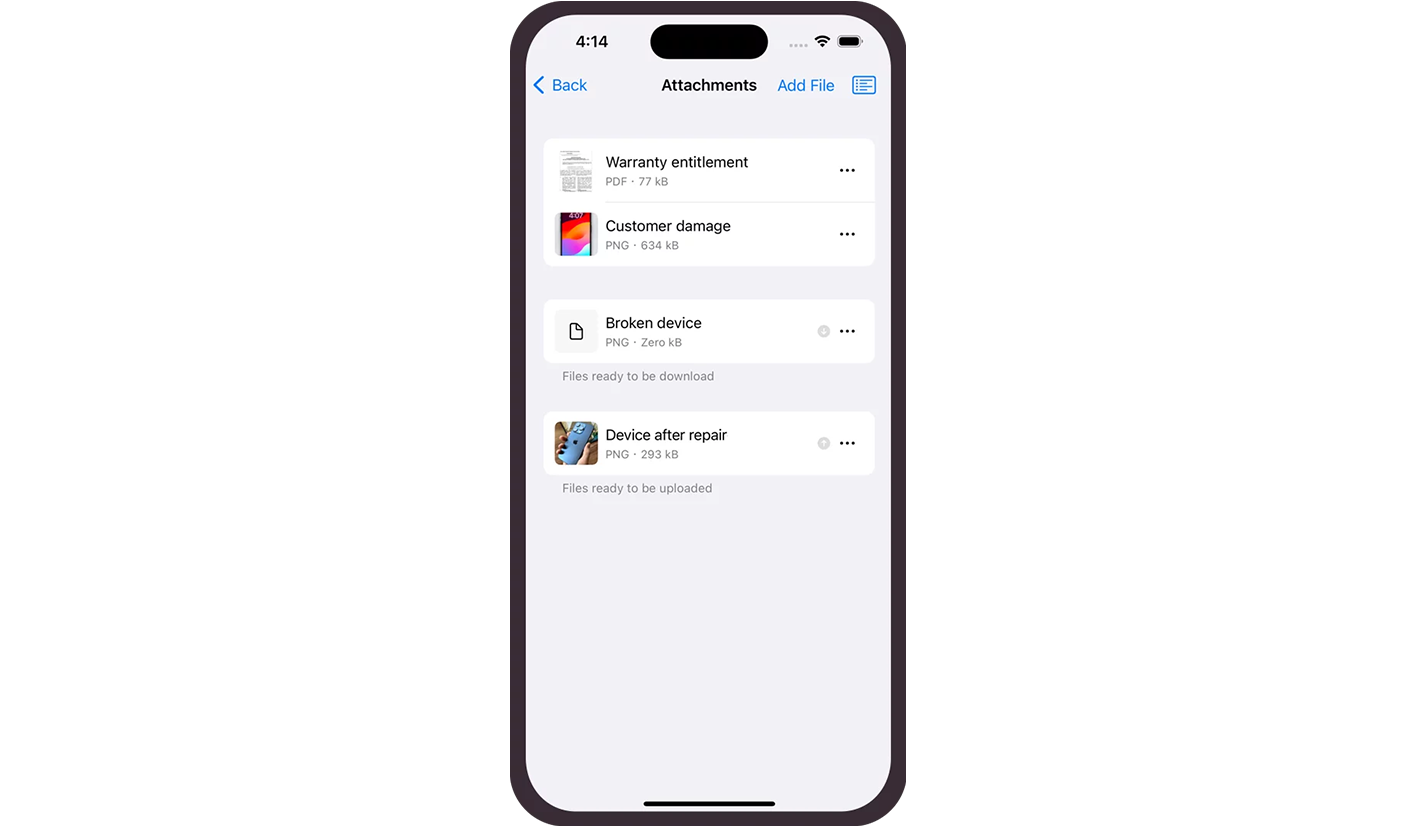
Frequently asked questions for manufacturing professionals
Fieldcode automates preventive maintenance scheduling and ensures technicians receive real-time service alerts, reducing unexpected equipment failures and keeping production lines running.
Fieldcode offers real-time inventory tracking and automated restocking alerts, ensuring that critical spare parts are always available—preventing production delays caused by missing components.
Our Zero-Touch automated scheduling assigns the best technician based on expertise, location, and urgency—cutting response times and improving first-time fix rates.
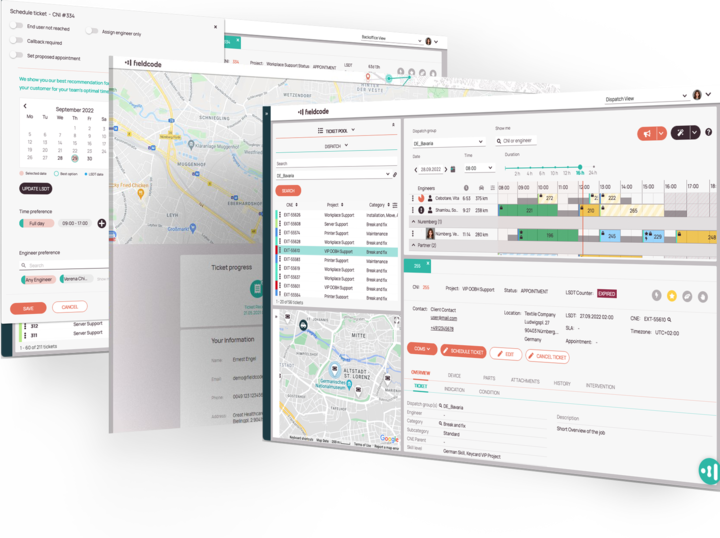
Last updated: 04.08.2025
See how Fieldcode maximizes uptime and efficiency
Prevent machine failures and service delays before they disrupt production. Request a demo, and our experts will show you how Fieldcode optimizes maintenance, streamlines service coordination, and keeps your production lines moving.