Achieving smartest field service for IoT providers - with IoT-driven field service
IoT vendors are well aware of the incredible potential of smart sensor technology, using it to help their clients improve efficiency and automate low-level, repetitive activities. When correctly configured, smart factories and workplaces deliver significant cost-savings and productivity gains.
But even the simplest smart sensors could be smarter.
IoT sensors do more than just one job
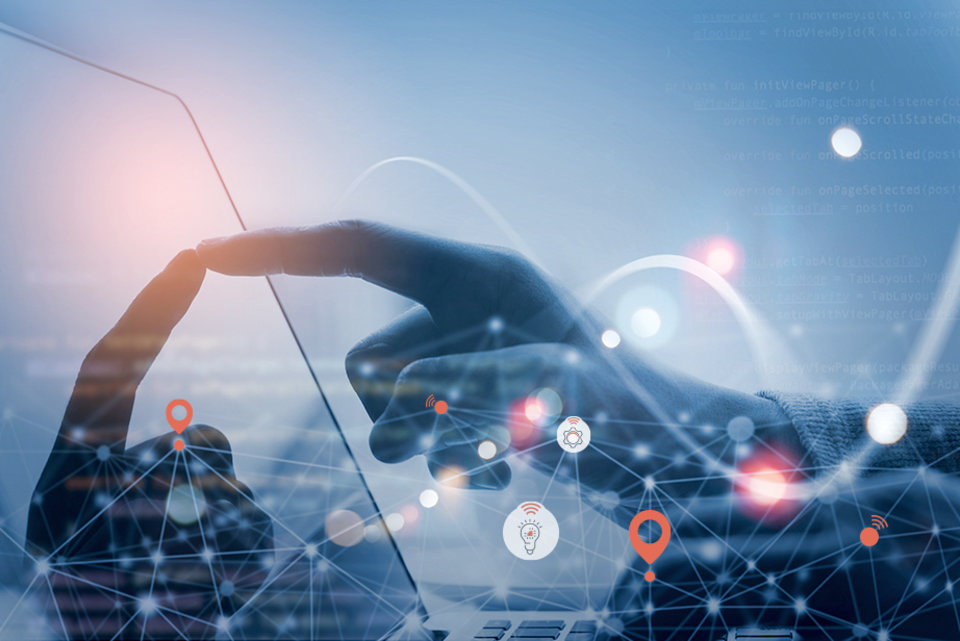
IoT deployments are usually focused on a single task – monitoring environmental factors or product quality control for instance. Automated production line systems are then configured to take action when certain thresholds are met. They will also alert the operator to errors and issues – and this is where IoT providers can enhance their offering.
For plant operators, IoT errors are their cue to contact you, the provider. This approach is slow, inefficient and potentially costly depending on how long it takes for the operator to report the issue, and for you to deploy a field engineer. But there is a better way.
Maximizing IoT potential
A far more efficient way of dealing with problems would be to forward non-operational alerts to the service provider as soon as they are generated. In this way, the provider has immediate notice of problems, allowing them to arrange an appropriate response more quickly.
Additional efficiency gains are available however. Using an IoT-enabled field service management platform allows you to automate the reporting and engineer dispatch process further still.
Automating your IoT field service response
Your field service management system should not only accept IoT input, but it should also apply logic to incoming notifications – just like your clients’ do during normal operations. The platform can then create and assign tickets automatically. An advanced platform will go further still, assigning tickets based on the most appropriate, available engineer.
Using automation in this way allows you to dispatch engineers before the client knows there is an issue – and without any additional manual effort from the field service manager. By streamlining and automating the reporting and dispatch process, some operators have reported cost savings of up to 40%, again demonstrating the value of IoT.
Seeing into the future
The data collected from your clients’ IoT sensors do not have to be restricted to failure alerts. You can also arrange to have status messages forwarded to your field service management platform, providing an overview of system health.
This data also allows you to establish a baseline against which alerts can be compared – automatically – in future. By analyzing IoT sensor trends, you can predict potential failures in advance. You can then schedule site visits by your field engineers before a client system fails entirely. Indeed, proactive maintenance that helps to avoid downtime will allow your business to charge a premium.
The truth is, IoT vendors already know what can be achieved by their clients using smart sensors. Now it’s time to use that technology to better serve them too.
To learn more about IoT and automated field service management, please get in touch to arrange a Fieldcode demo.